Ketahanan air yang buruk, permukaan yang tidak rata, kandungan bubuk yang tinggi, dan panjang yang tidak merata? Masalah umum dan langkah-langkah perbaikan dalam produksi pakan akuatik.
Dalam produksi pakan akuatik harian kami, kami menghadapi beberapa masalah dari berbagai aspek. Berikut beberapa contoh yang dapat kami diskusikan dengan Anda semua:
1. Rumus
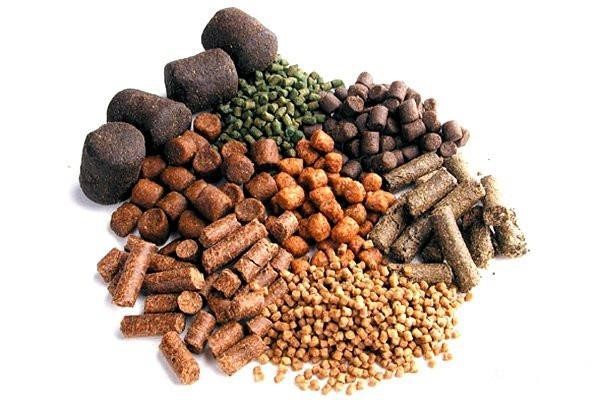
1. Dalam struktur formula pakan ikan, terdapat lebih banyak jenis bahan baku tepung, seperti bungkil rapeseed, bungkil kapas, dll., yang tergolong serat kasar. Beberapa pabrik minyak memiliki teknologi canggih, dan minyak pada dasarnya digoreng kering dengan kandungan yang sangat sedikit. Selain itu, bahan baku ini tidak mudah diserap dalam proses produksi, yang berdampak besar pada granulasi. Selain itu, bungkil kapas sulit dihancurkan, sehingga memengaruhi efisiensi.
2. Solusi: Penggunaan bungkil rapeseed telah ditingkatkan, dan bahan-bahan lokal berkualitas tinggi seperti dedak padi telah ditambahkan ke dalam formula. Selain itu, gandum, yang jumlahnya sekitar 5-8% dari formula, telah ditambahkan. Melalui penyesuaian, efek granulasi pada tahun 2009 relatif ideal, dan rendemen per ton juga meningkat. Partikel berukuran 2,5 mm memiliki berat antara 8-9 ton, meningkat hampir 2 ton dibandingkan sebelumnya. Penampilan partikel juga telah meningkat secara signifikan.
Selain itu, untuk meningkatkan efisiensi penghancuran bungkil biji kapas, kami mencampur bungkil biji kapas dan bungkil rapeseed dengan rasio 2:1 sebelum penghancuran. Setelah perbaikan, kecepatan penghancuran pada dasarnya setara dengan kecepatan penghancuran bungkil rapeseed.
2. Permukaan partikel tidak rata
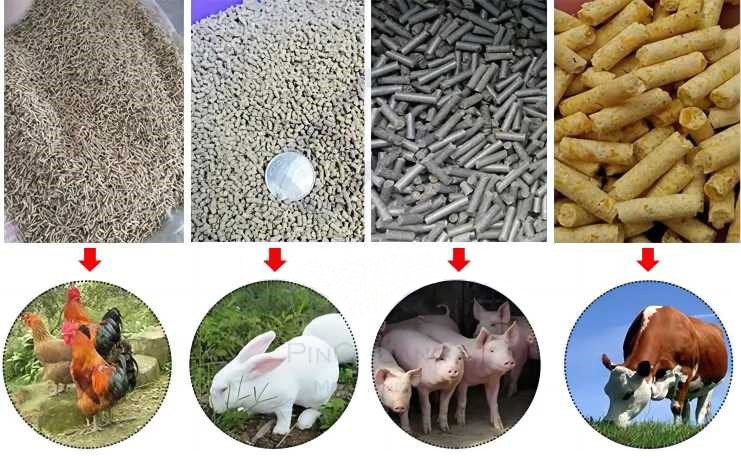
1. Ini memiliki dampak besar pada penampilan produk jadi, dan ketika ditambahkan ke air, rentan terhadap kerusakan dan memiliki tingkat pemanfaatan yang rendah. Alasan utamanya adalah:
(1) Bahan baku dihancurkan terlalu kasar, dan selama proses temper, bahan baku tidak sepenuhnya matang dan melunak, dan tidak dapat dikombinasikan dengan baik dengan bahan baku lainnya saat melewati lubang cetakan.
(2) Pada formula pakan ikan dengan kandungan serat kasar tinggi, karena adanya gelembung-gelembung uap pada bahan baku saat proses tempering, gelembung-gelembung tersebut pecah akibat adanya perbedaan tekanan antara bagian dalam dan luar cetakan pada saat pengempaan partikel, sehingga mengakibatkan permukaan partikel tidak rata.
2. Tindakan penanganan:
(1) Kontrol proses penghancuran dengan benar
Saat ini, dalam produksi pakan ikan, perusahaan kami menggunakan serbuk mikro ayakan 1,2 mm sebagai bahan baku curah. Kami mengontrol frekuensi penggunaan ayakan dan tingkat keausan palu untuk memastikan kehalusan penghancuran.
(2) Kontrol tekanan uap
Sesuai formula, sesuaikan tekanan uap secara wajar selama produksi, umumnya berkisar sekitar 0,2. Karena tingginya kandungan serat kasar dalam formula pakan ikan, diperlukan uap berkualitas tinggi dan waktu tempering yang wajar.
3. Ketahanan partikel terhadap air buruk
1. Jenis masalah ini adalah yang paling umum dalam produksi harian kita, umumnya terkait dengan faktor-faktor berikut:
(1) Waktu tempering yang pendek dan suhu tempering yang rendah menyebabkan tempering tidak merata atau tidak mencukupi, tingkat pematangan rendah, dan kadar air tidak mencukupi.
(2) Bahan perekat seperti kanji kurang memadai.
(3) Rasio kompresi cetakan cincin terlalu rendah.
(4) Kandungan minyak dan proporsi bahan baku serat kasar dalam formula terlalu tinggi.
(5) Faktor ukuran partikel penghancur.
2. Tindakan penanganan:
(1) Meningkatkan kualitas uap, menyesuaikan sudut bilah regulator, memperpanjang waktu temper, dan meningkatkan kadar air bahan baku secara tepat.
(2) Sesuaikan formula, tingkatkan bahan baku pati secara tepat, dan kurangi proporsi bahan baku lemak dan serat kasar.
(3) Tambahkan perekat jika perlu. (Bubur bentonit berbahan dasar natrium)
(4) Meningkatkan rasio kompresicetakan cincin
(5) Mengontrol kehalusan sumur penghancur
4. Kandungan bubuk yang berlebihan dalam partikel
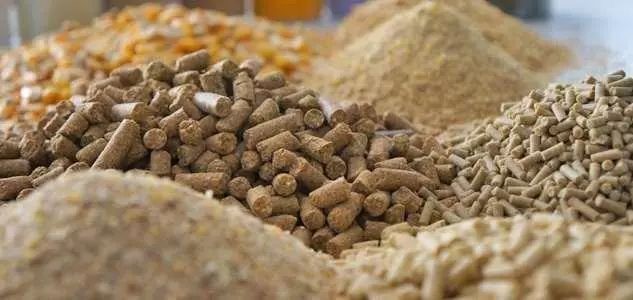
1. Sulit untuk memastikan tampilan pakan pelet secara umum setelah pendinginan dan sebelum penyaringan. Pelanggan melaporkan bahwa terdapat lebih banyak abu dan bubuk halus di dalam pelet. Berdasarkan analisis di atas, saya rasa ada beberapa alasan untuk hal ini:
A. Permukaan partikel tidak halus, sayatan tidak rapi, dan partikelnya longgar dan mudah terbentuk bubuk;
B. Penyaringan yang tidak sempurna dengan penyaringan bertingkat, kasa saringan tersumbat, bola karet aus parah, lubang kasa saringan tidak pas, dan sebagainya;
C. Terdapat banyak residu abu halus di gudang produk jadi, dan pembersihannya tidak menyeluruh;
D. Ada bahaya tersembunyi dalam penghilangan debu selama pengemasan dan penimbangan;
Tindakan penanganan:
A. Optimalkan struktur formula, pilih ring die secara wajar, dan kendalikan rasio kompresi dengan baik.
B. Selama proses granulasi, kendalikan waktu tempering, jumlah pengumpanan, dan suhu granulasi untuk mematangkan dan melunakkan bahan baku sepenuhnya.
C. Pastikan penampang partikel rapi dan gunakan pisau pemotong lunak yang terbuat dari strip baja.
D. Sesuaikan dan rawat layar pemeringkatan, dan gunakan konfigurasi layar yang wajar.
E. Penggunaan teknologi penyaringan sekunder di bawah gudang produk jadi dapat mengurangi rasio kandungan bubuk secara signifikan.
F. Gudang dan sirkuit produk jadi perlu dibersihkan tepat waktu. Selain itu, perlu ditingkatkan kualitas pengemasan dan perangkat penghilang debu. Sebaiknya gunakan tekanan negatif untuk penghilang debu, yang lebih ideal. Terutama selama proses pengemasan, pekerja pengemasan harus secara teratur mengetuk dan membersihkan debu dari hopper penyangga timbangan pengemasan..
5. Panjang partikel bervariasi
1. Dalam produksi sehari-hari, kami sering mengalami kesulitan dalam pengendalian, terutama untuk model di atas 420. Alasannya secara garis besar adalah sebagai berikut:
(1) Jumlah pemberian pakan untuk granulasi tidak merata, dan efek tempering sangat berfluktuasi.
(2) Kesenjangan yang tidak konsisten antara rol cetakan atau keausan parah pada cetakan cincin dan rol tekanan.
(3) Sepanjang arah aksial cetakan cincin, kecepatan pembuangan di kedua ujungnya lebih rendah daripada di tengah.
(4) Lubang pengurang tekanan cetakan cincin terlalu besar, dan laju pembukaan terlalu tinggi.
(5) Posisi dan sudut bilah pemotong tidak masuk akal.
(6) Suhu granulasi.
(7) Jenis dan tinggi efektif (lebar bilah, lebar) bilah pemotong cincin memiliki dampak.
(8) Pada saat yang sama, distribusi bahan baku di dalam ruang kompresi tidak merata.
2. Kualitas pakan dan pelet umumnya dianalisis berdasarkan kualitas internal dan eksternalnya. Sebagai sistem produksi, kita lebih banyak terpapar pada hal-hal yang berkaitan dengan kualitas eksternal pelet pakan. Dari perspektif produksi, faktor-faktor yang memengaruhi kualitas pelet pakan akuatik dapat diringkas secara garis besar sebagai berikut:
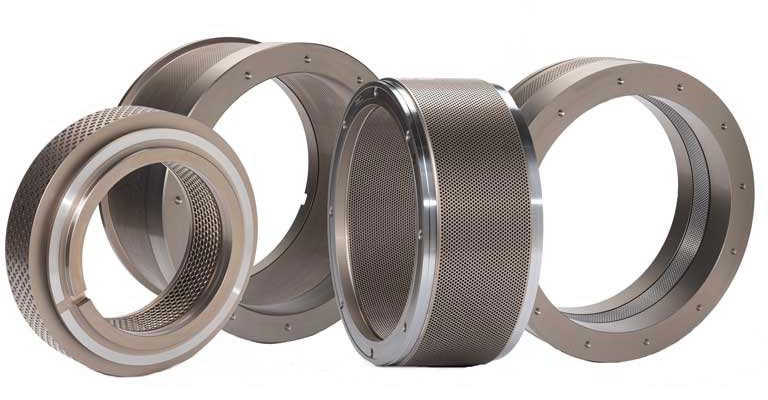
(1) Desain dan pengaturan formula mempunyai pengaruh langsung terhadap kualitas pelet pakan akuatik, yaitu sekitar 40% dari total;
(2) Intensitas penghancuran dan keseragaman ukuran partikel;
(3) Diameter, rasio kompresi, dan kecepatan linier cetakan cincin berdampak pada panjang dan diameter partikel;
(4) Rasio kompresi, kecepatan linier, efek pendinginan dan temper cetakan cincin, dan pengaruh bilah pemotong terhadap panjang partikel;
(5) Kadar air bahan baku, efek tempering, pendinginan dan pengeringan mempunyai pengaruh terhadap kadar air dan penampakan produk jadi;
(6) Peralatan itu sendiri, faktor proses, dan efek pendinginan dan tempering memiliki dampak pada kandungan bubuk partikel;
3. Tindakan penanganan:
(1) Sesuaikan panjang, lebar, dan sudut pengikis kain, dan ganti pengikis yang aus.
(2) Perhatikan penyesuaian posisi pisau pemotong tepat waktu di awal dan menjelang akhir produksi karena jumlah pengumpanan yang kecil.
(3) Selama proses produksi, pastikan laju pengumpanan dan pasokan uap stabil. Jika tekanan uap rendah dan suhu tidak dapat naik, segera sesuaikan atau hentikan.
(4) Sesuaikan celah antara kedua sisi secara wajarcangkang rolPasang kembali cetakan baru dengan rol baru, dan segera perbaiki permukaan rol penekan dan cetakan cincin yang tidak rata akibat keausan.
(5) Perbaiki lubang pemandu cetakan cincin dan segera bersihkan lubang cetakan yang tersumbat.
(6) Saat memesan cetakan cincin, rasio kompresi tiga baris lubang di kedua ujung arah aksial cetakan cincin asli bisa 1-2 mm lebih kecil dari yang di tengah.
(7) Gunakan pisau pemotong yang lembut, dengan ketebalan yang dikontrol antara 0,5-1mm, untuk memastikan ujung yang tajam sebanyak mungkin, sehingga berada pada garis penyambungan antara cetakan cincin dan rol tekanan.
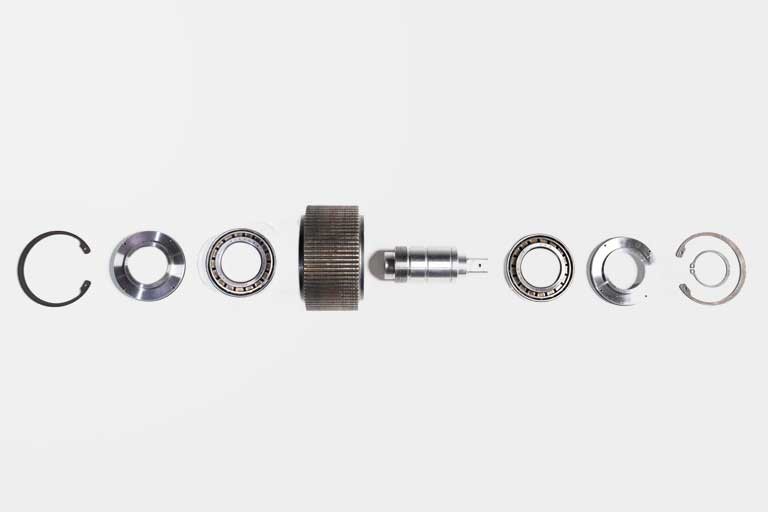
(8) Pastikan konsentrisitas cetakan cincin, periksa jarak bebas spindel granulator secara teratur, dan sesuaikan jika perlu.
6. Ringkasan Titik kontrol:
1. Penggilingan: Kehalusan penggilingan harus dikontrol sesuai dengan persyaratan spesifikasi
2. Pencampuran: Keseragaman pencampuran bahan baku harus dikontrol untuk memastikan jumlah pencampuran yang tepat, waktu pencampuran, kadar air, dan suhu.
3. Pematangan: Tekanan, suhu, dan kelembaban mesin puffing harus dikontrol
Ukuran dan bentuk bahan partikel: spesifikasi cetakan kompresi dan pisau pemotong yang sesuai harus dipilih.
5. Kadar air pakan jadi: Perlu diperhatikan waktu dan suhu pengeringan dan pendinginan.
6. Penyemprotan minyak: Penting untuk mengontrol jumlah penyemprotan minyak yang tepat, jumlah nosel, dan kualitas minyak.
7. Penyaringan: Pilih ukuran saringan sesuai dengan spesifikasi material.
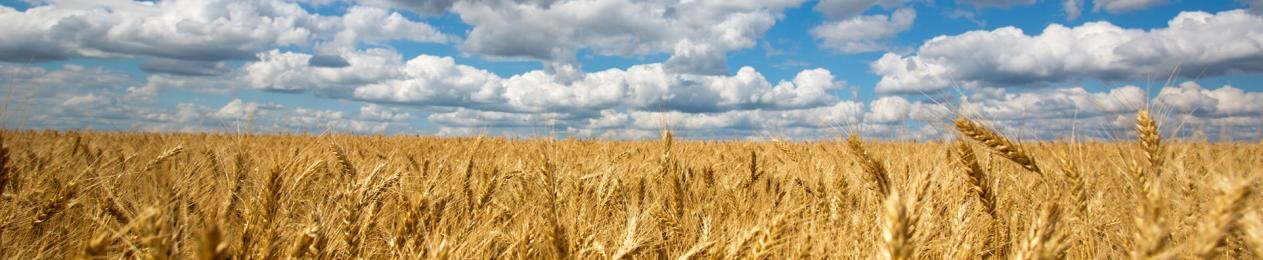
Waktu posting: 30-Nov-2023